A few decades ago most couches and sofas built in the U.S. were made in small shops with 50 or fewer employees. Products were primarily built one piece at a time by a single highly skilled upholsterer working on an entire piece.
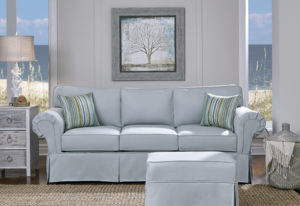
Most of the upholstered furniture seen in large U.S. chain retailers today is mass produced in huge factories. Production of huge quantities of identical items is most efficiently done in cells where lower skilled (low-paid) workers are assigned to build a single small part of each couch over and over again.For example a furniture manufacturing cell (group of workers building a single piece) in a large factory might consist of one worker who upholstered only outside arms, another inside arms, another outside backs, another inside backs, etc.Designs must be simple so that fabric covers can be pre-sewn and “socked on” over each part of the sofa. This allows each individual component to be upholstered quickly by workers with minimal skills.30 years ago the top 25 furniture retailers controlled less than 10% of U.S. nationwide furniture sales. A retailer could join this group with annual sales of less than $50 million. Today, the top 25 retailers account for 80% of nationwide furniture purchases. The smallest of these has $675 million in annual sales.
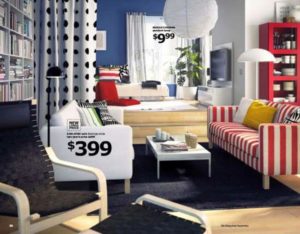
Modern mass produced sofas are assembled (with variations) as follows: First, you build a frame, which be made of plywood, composite wood products or cheap solid wood (typically rubberwood in Asia and pine in Europe), joined via various joinery techniques plus staples and/or screws and other hardware.A flexible support surface is needed for the sitting area and the back area. You can employ several materials, but among the most used because of its cheap nature are special composite elastic fabric bands which are stapled evenly to the frame via a nail gun.An alternative would be S-shaped (also known as sinuous wire or zig zag) springs. This basic structure could be covered also with a layer of non-woven sheet of protective fabric.This basic sofa frame is covered with padding and cushions. There are many different alternatives methods and materials depending on the style and shape of the sofa.
The cheapest method is often to cut pre-formed shapes from polyurethane foam and combine them to create different looks, gluing them together as you need to create the basic shapes.
Next comes the covering for the sofa. Fabric covers, which have been pre-cut and sewn earlier, are now applied to the sofa and glued, stitched or stapled to make them fit onto the frame and the upholstery.
Cushions are made separately. When producing thousands of pieces, even small cost savings in materials or reduced labor time can add up.
These costs may be minimized by using the least expensive foam that will hold up through the warranty period.
Cushions have a foam or spring core, usually with a dacron fiber wrapping over the foam. Sometimes a fabric ticking goes over the foam and beneath the fabric cover.
The cushion inserts are stuffed through the tiny zippers using huge pneumatic machinery that reduces the time required for stuffing cushions from several minutes manually to just a few seconds.
Next, the sofa is fitted with the legs, which may be built into the frame but are more typically screwed into the base. Some styles use a wood or metal support frame.)
Last comes the final touches, like covering the bottom of the sofa by stapling a sheet of non-woven textile to preserve it from dust.
Higher end couches use more expensive materials and may require more workmanship and skill to properly prepare and setup, but this would be like an add-on to the basic technique outlined above.
Frames can be made from a variety of different materials. Each material is typically available in many different variations and qualities.
For example plywood that is 7 plies with a total thickness of 1” is far stronger than 0.5” plywood made with three plies.
Engineered hardwood covers a broad category of materials. Lower cost frames may use medium-density fiberboard (MDF), particle board, or inexpensive plywood.
In general the thicker the wood or wood product is, the stronger the frame will be. For example high end solid wood frames are typically 5/4” thick while less expensive solid wood frames are 4/4” or less.
Wood species makes a difference also. Maple is the furniture of choice for most high end sofa frame makers. Maple is hard enough to last for a very long time while being soft enough so that it is easy to work with.
Harder woods such as oak or hickory make excellent frames but are more to work with. Softer woods such as poplar, birch or pine are easy to work with but are not as strong. Frames made with these softer woods are rarely found in 5/4” thicknesses or used in high end furniture.
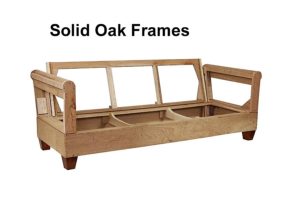
Another factor is the quality of the lumber. #2 grade lumber will have far more knotholes, splits and imperfections than #1 grade or Select (the highest grade.)
Kiln-drying is important for several reasons. Green (undried)lumber tends to warp over time. Cracks, knotholes and other imperfections can widen, sometimes to the point of frame failure.
How can you tell what kind of wood was used in your sofa. Try lifting one end. Better quality frames are heavier. 5/4” solid wood frames are extremely heavy.
Frames are made by joining pieces of wood together. After lumber imperfections, the joints are typically the weakest part of the frame.
Different types of joints include:
Mortise & Tenon: The strongest method, this is used when two pieces of wood meet at a 90 degree angle. One piece of wood has a hole and the other is cut to fit precisely into that hole.
Double Dowel: A dowel is a small, wooden cylinder. It gets inserted into a small round hole drilled into two pieces of wood to hold them together. A double dowel is just what it sounds like: two wood dowels at each joint. While not as sturdy as a mortise and tendon, and more likely to loosen over time, this is still a perfectly acceptable method that is found on many upholstery frames.
Corner Block Reinforced: Corners are weak points on wood furniture and need to be reinforced. An extra piece of wood (usually triangular) is placed at an angle, glued and stapled or screwed into place.
Reinforced Joinery: This describes adding an extra layer of support to keep things in place. The joint could be reinforced with glue, screws, or staples.
Other Joinery Methods: There are many other ways of joining furniture, some good (dovetail and box joints are used when building cabinetry and wood furniture) and some not as good, for example a butt joint, where two pieces of wood are put together with only glue, screws, or a combination of the two, or metal connectors that are attached to two pieces of wood.
Spring Systems
The 8-way hand-tied spring is a mark of quality and has been considered the “gold standard” for over a century.
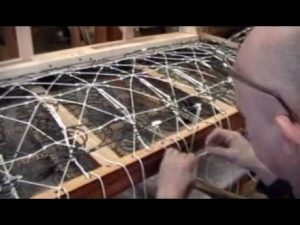
8 way hand tied spring foundations were invented at a time in which cushion materials were things like horsehair, down/feathers and cotton. These are all non-resilient materials.
Cushions made with non-resilient materials can sink all the way down to the sofa deck. When that happens the 8 way hand tied coil is the best foundation available.
Today’s high density foam cushions are far more resilient (and significantly thicker) than the old cushions made with the older fillings. The result is that you do not sink all the way to the deck where you feel the foundation underneath.
The hundreds of dollars extra that the 8 way hand tied coils cost are mostly wasted since you won’t be able to feel them when you sit.
Drawbacks of 8 way hand tied coils (aside from cost) include:
• They do not last any longer than many far less expensive foundation options.
• Many modern styles are built lower to the ground and do not have enough space underneath to accommodate the 8 way coils.
• Many companies now use drop-in coil systems which resemble 8 way hand tied, but are far less costly to make and do not provide the same level of comfort.It is very difficult for a non-expert to distinguish between these drop-in units and the real thing.

Sinuous wire (also known as Zig-zag springs) are an S-shape, simpler in construction and very inexpensive. They are attached to the frame, with clips and usually last just as long (or longer) than the far more expensive 8 way hand tied coil foundation
Webbing is another alternative, which can be a very poor support or a very good support depending on the quality of the webbing, the width, how many strips are used and the strength of the frame.Webbing comes in different width strips which are stretched across the deck (or frame) and woven back and forth like the reed strips in a basket.Higher priced sofas with webbing foundations typically have more strips (and smaller gaps) than couches that are less expensive.Jute webbing may be found in older sofas. Jute is not as durable or flexible as the newer elasticized webbing materials.Elasticized webbing can also be used for support of the back frame.
Cushion construction is the single most important factor in determining the lifespan (and comfort) of your sofa, couch or chair.
On low and mid-priced furniture, the cushions are almost always the first part of a sofa or couch that will wear out and need replacement. On higher cost sofas, fabrics (particularly natural fibers like cotton or linen) may wear out sooner.
Most cushions sold on low and mid-priced upholstered furniture will begin to lose their shape and comfort within 1 – 3 years and will need replacement within 3-5 years.
For most mass produced sofas, cushion replacement is not a realistic option. Replacement cushions are rarely available from the retailer where the furniture was purchased. Custom replacement cushions can be expensive.
There are three basic types of cushion construction for most couches and sofas sold in the U.S.
• Foam
• Coil springs
• Down/feathers
Many cushions are made using a combination of two or all three of these various constructions.
Foam is the most commonly sold cushion construction. It is available in several different densities.
Each foam density is available in a wide variety of different firmnesses.
Although most people think that density and firmness are synonymous they are actually very different.
Most foam suppliers typically stock 4-5 commonly used densities for residential furniture seat cushions ranging from 1.5 to 2.5. The number designates the weight (in pounds) of 1 cubic ft. of foam.
Each of these different densities may be available in 10 or more different firmnesses ranging from very soft to very firm.
The expected lifespan of a foam cushion is primarily dependent on the density and thickness of the foam.
Another important factor is whether the foam is HR (High Resiliency) which recovers its shape better after use.
The frequency of use and the size of the people using the cushion will also affect a seat cushion’s lifespan.
A foam cushion’s “firmness” has very little effect on the expected lifespan, however since most consumers equate “firmness” with durability, cheap foams are often made “extra firm.” With a low density foam, that “extra firm” feeling will not last long.
Foams used in seat cushions for moderately priced residential furniture generally range from 1.5 through 2.0.
Lower density foams are typically used for back cushions or padding that goes over the arms or other parts of the frame.
Higher densities (2.0 – 2.5) can be found on more expensive residential furniture.
Furniture designed for heavy commercial or institutional use may use foam with densities of 3.0 or higher.
The higher the foam density the more the cushion will cost. Variations in firmness usually do not affect cost. HR (High Resilience) foam is more expensive than non-HR foams.
The most commonly used foam density for residential furniture sold in the U.S. is 1.8.
Foam that is described as “High Density” without any specific number is usually 1.8 density foam.
Foam cores are usually anywhere from 4″ – 6″ thick and is typically wrapped in a dacron polyester fiber.
Fiber wrapping is generally 0.5 – 1.5″ thick on the top and bottom of the cushion.
It softens the feel of the cushion and will add 2-3″ to the total cushion thickness, but has no effect on lifespan.
4″ thick foam cores made with 1.8 density HR (High Resiliency) foam can be expected to last about 2 years with average use before the foam begins to lose its ability to bounce back and keep its shape.
5″ thick foam cores made with 1.8 density HR (High Resiliency) foam can be expected to last about 3 years with average use before the foam begins to lose its ability to bounce back and keep its shape.
Foam cushions will typically still be usable for another couple of years after the deterioration process begins.Foams that are not High Resiliency will deteriorate more rapidly.
Actual foam densities will vary during the manufacturing process. A variation of 0.1 is considered normal. A 1.8 density foam may actually be 1.7 or 1.9. Larger variations are not unusual.
There are many couches sold with cheaper (and lighter weight) 1.5 density foam that will deteriorate even more rapidly, sometimes within one year of purchase.
The overall thickness of a cushion may or may not be an indication of a cushion’s durability.
“Value priced” couches will sometimes have cushions that are bulked up with several inches of polyester fiber around the foam core.
That polyester fiber will rapidly compress causing the cushion to lose its shape. Better quality sofas typically use 1″ – 1.5″ of fiber on each side of the cushion.
Lower quality couches may use up to 3″ of fiber on each side. Thick layers of fiber are a cheap way to bulk up a cushion over the short term. Thick fiber quickly compresses and causes the cushion to lose its shape – often within one year.
If you want to get more than 5 years of use from your couch you will need to find a couch with a better quality cushion.
Higher priced couches generally use thick higher density foams with at least a 2.0 density. but preferably higher.
Cushions supported by built-in coil springs are typically (but not always) more durable than lower density foam cushions.
These coil springs are surrounded by a foam border (which is typically 1.5 or 1.8 density) and then padded on the top and bottom with additional soft padding.
Down/feathers are often used as the padding in combination with coil springs. A down/feather “jacket” is used as a layer of padding on the top and bottom to soften the feel of the cushion.
Other common types of padding used in combination with coil spring cushions are memory foam and polyester fiber.
Down blend cushions use Down/feathers in combination with a foam core cushion. Down blend cushions have a shorter lifespan when compared with a solid slab of similar density foam.
When down/feathers are used with either coil springs or foam cores the mixture is typically 5% (or less) down and the remainder feathers. Down is far more expensive than feathers. Goose down is more expensive than duck down.
More expensive furniture may use higher percentages of down. Down is much softer and plush than feathers.
100% Down/feather cushions were extremely popular in the 18th, 19th and early 20th centuries. They are far less common today, both because of the high cost and the need to fluff up the cushions every time you stand up. Down/feathers have no “resilience” and do not “bounce back” by themselves after use like foam or coil springs.
Regardless of the price that you paid for your cushions they are rarely covered under Warranty.
Warranties (including extended warranties) are usually written so that anything that happens is considered “normal wear” — even when those cushions begin to visibly deteriorate in less than 1 year.
When shopping for a couch always test the cushions by picking them up. As a general rule if the seat cushions feel “light” you are looking at a couch with a very short expected lifespan.
Padding is the material that goes over the frame and directly under the upholstery fabric. Its function is to fill out and firm up the contours of the sofa or chair (fully upholstered) so that the fabric sits smoothly and fits perfectly all around, without wrinkles or puckers.
Insufficient padding can result in feeling the uncomfortable hardness of the frame.
Padding also acts as a buffer along the arms and back of a piece where friction and wear show up first, as on corners and edges. Foam or cotton padding are often used, sometimes mixed with other insulating materials.
Cheaper upholstered furniture sometimes uses cardboard as a padding material over the arms rather than the more expensive foam.
Padding comes in different grades and a thickness of about 1¾” is considered a good padding. Polyester fiberfill is also currently being used as a padding and is providing excellent results.
There are many thousands of fabrics available and hundreds more are introduced every month. Fabric prices can vary widely, with wholesale prices paid by manufacturers ranging from $2/yd. to $100/yd. or more.
Typically, using a $50/yd. fabric will increase the retail price of an average size sofa by approximately $600 – $800 compared with a $5/yd. fabric.
Most consumers do not realize that even high end manufacturers will often offer fabrics that they purchased in the $5 – $10/yd. price range in addition to far more expensive options.
Natural fibers such as cotton, linen and wool are generally less durable and not as easy to clean as synthetic fabrics.
Synthetics such as 100% polyesters and 100% olefins are currently an extremely popular choice, combining durability, cleanability and low price.
Blends of synthetics and natural fibers can get significantly more expensive while retaining durability and cleanability.
Fibers also make a difference in durability. Natural fibers, like cotton, take color differently from man-made fibers. They can be richer, more subtle while the synthetics have resilience and strength.
Blends combine properties of both natural and synthetic fibers. Cotton blended with polyester, for example, can give you the best attributes of both. Other common blends may use nylon, acrylic, rayon, wool or silk.
Technology for man-made fibers has advanced tremendously over the past decade. 100% polyesters can now imitate the look and feel of cottons, linens, suedes, velvets, wool, silk and other materials.
Fabric durability is also affected by the weight and weave of the fibers. The standard is threads to the inch. One square inch of fabric with 8 or 10 thick threads doesn’t have the strength of one square inch densely packed with 30 to 40 thin threads.
For example a heavy woven cotton tapestry, where the colors and pattern are tightly woven in with colored threads, wears better than a cotton with the colors printed on. To check a fabric yourself, hold it up to the light. The less light that shows through, the tighter the weave.
Over the past decade a new category of fabrics has begun to take a larger and larger percentage of the fabric market. These are the high performance fabrics that combine heavy-duty durability with stainproofing technology.
Popular high performance brands include Crypton, Sunbrella and Revolution. The vast majority of High Performance fabrics are currently made in the U.S. They are beginning to bring back a textile industry that was almost extinct as mills moved to China beginning in the 1990s.
The appearance of certain textures can vary with use. Fabrics with a nap, like velvets and corduroys, look different in different lights, and show wear where they’ve been sat upon. Silks are more delicate, but many are fortified with a man-made fiber. And fabrics with highly textured surfaces, like loopy tweeds and homespuns can “pull” after a while.
Fabric can completely transform the look of a sofa. It can change a sofa with an identical frame from traditional to modern. It can blend into the room or accent it. Fabric is the most obvious sign of your personal taste and style.
Leather is very different than fabric, both as a material and in terms of manufacturing requirements. Leathers range from expensive to extremely expensive.
Leather is made from animal hides. These hides come in irregular shapes and sizes. There is typically a high percentage of waste when leather is being cut.
Holes, brands, insect bites and other flaws can result in high percentages of unusable material which varies tremendously from hide to hide.
Every aspect of manufacturing takes far longer when working with leather. Cutting the material, sewing it and upholstering all take far longer than is needed for fabric.
Different sewing equipment is needed. It also requires greater skill and experience. Mistakes can be very expensive to the company making leather furniture.
There are hundreds of different types of leathers, which are available in a tremendous range of prices that can vary by thousands of dollars.
The least expensive are the “protected” leathers. These are cheaper hides with many flaws that are heavily dyed and processed. The processing actually removes the natural grain, which is then synthetically restored.
The most expensive leathers are the natural leathers, which have no processing and show all natural flaws. They have no protective coating.
Expensive computerized cutting machinery can significantly reduce the amount of waste that is inevitable in the manual cutting process. Only large manufacturers can afford this.
Know someone who might be interested in this post? Please like and share this post with them. If you have questions or comments please leave them below.